Freeman's Guide To Abrasives Part 1 of 2: Abrasives Overview
Go directly to Part 2: Freeman's Line of Abrasives
Abrasives are most commonly used to precisely remove small amounts of material to achieve a specific dimension, smooth or polish a surface, or roughen materials for gluing applications.
When selecting the proper abrasive for an application, the following criteria need to be considered…
#1 - Type of abrasive required:
This decision is made by knowing what type of material you will be working with.
|
|
|
Garnet - A reddish brown mineral. It is of medium hardness with good cutting edges and has the tendency to break or fracture when used, thus creating new cutting edges. Used primarily for fine finishing of wood. |
Aluminum Oxide - A synthetic brown-colored mineral that is tough and durable and is the most widely used abrasive grain. It is ideal for both woodworking and metalworking. (Non-Ferrous) |
Silicon Carbide - A very hard and shiny black-colored mineral. This product has a brittle quality that allows it to fracture into sharp sliver-like wedges as it works. Can be used for everything from sanding non-ferrous and ferrous metals, plastics, composites, and wood products. |
#2 - Type of backing required:
This decision is made by the type of abrasive and grit you have selected or the type of process you will be performing with the abrasive.
|
|
Paper - Used mainly for wood finishing in weights from A, C, D, E and F. “A” is the lightest weight. |
Cloth - Produces a flexible backing in a wide range of weights. The more popular “J” and “X” weights are standard stock items. The “J” weight is the lightest and most flexible whereas the “X” weight is a heavier backing providing the widest range of use. |
#3 - Type of glue required:
This decision is made by the type of abrasive you have selected or the type of process you will be performing.
- Glue - A straight animal hide glue that is used to adhere the abrasive particles to the backing. Referred to as “Glue Bond”.
- Resin - A synthetic resin that is used to adhere the abrasive particles to the backing. This type of bond is resistant to heat and moisture and is referred to as “Resin Bond”.
#4 - Coarseness of the abrasive mineral:
Commonly referred to as “grit”, this number designation is determined by the amount of abrasive mineral that can pass through a mesh screen with specific size openings. Therefore, a 40 grit abrasive particle will pass through a mesh screen that has 40 openings in one linear inch.
Consequently, the higher the “grit” number results in a finer abrasive and will produce a smoother surface finish. The lower the “grit” number results in a coarser abrasive that will remove material much faster.
#5 - Amount of abrasive applied:
This decision is made by knowing the type of material you will be working with.
- Open Coat – Here, the abrasive granules cover from 50% - 70% of the backing and are set at pre-determined spacing to reduce loading. Used on softer surface materials that tends to load or fill the abrasive surface.
- Closed Coat – Here, the abrasive granules cover virtually the entire backing surface. Used where loading of abrasives is less of a problem.
#6 - Form and shape of the abrasive:
This decision is made by determining how the abrasive will be used by the individual. Abrasives are sold in forms such as sheets, large/small discs, belts, and large/small rolls. Selecting the right form is determined by whether the abrasive will be used for hand sanding, applied to a large disc sander, attached to a small hand grinder, or installed on a large belt sanding machine.
Sanding of concave shapes probably requires round or cylindrical shaped abrasives. Flat or convex shapes probably require flat abrasives.
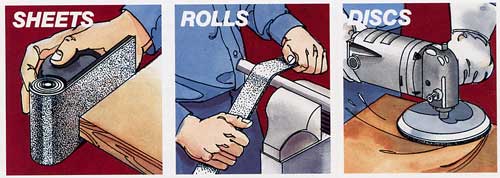
Continue to Part 2 of 2: Freeman's Line of Abrasives
|